Pretreatment System

Pretreatment System
A Pretreatment System is an essential part of any paint shop, designed to prepare surfaces for painting by removing contaminants like dirt, oil, and rust while improving paint adhesion. This process not only ensures a smooth and durable finish but also enhances corrosion resistance.
Why Pretreatment is Important: Before any painting process, the surface must be clean and prepared to ensure optimal paint adhesion. Without proper pretreatment, the paint could peel, crack, or fail prematurely. A pretreatment system helps to:
-
Improve paint adhesion
-
Enhance the durability and lifespan of the paint
-
Increase corrosion resistance
-
Provide a uniform surface for better coating application

Types of Pretreatment Systems
-
Spray Pretreatment Systems:
-
Ideal for large parts, spray systems apply chemicals through a series of spray nozzles, ensuring even coverage across the entire surface. These systems are automated and suitable for high-volume production.
-
-
Dip Pretreatment Systems:
-
Dip systems are used for smaller or more intricate parts, submerging them in chemical baths to achieve comprehensive surface coverage. These systems are often used in batch processing or for complex geometries
-

Key Stages
Key Stages of the Pretreatment Process:
-
Degreasing & Cleaning:
-
The first step involves removing oils, grease, dirt, and other contaminants from the surface using either a hot alkaline solution or solvents. This ensures the surface is clean and ready for the next steps.
-
-
Rinsing:
-
After cleaning, the component is thoroughly rinsed with water to remove any chemical residues. This helps to prevent contamination in the subsequent steps.
-
-
Surface Conditioning:
-
In this stage, a conditioning agent is applied to activate the surface for the conversion coating process, promoting uniform coating application.
-
-
Phosphating / Conversion Coating:
-
A phosphate or zirconium-based solution is applied to form a corrosion-resistant layer on the metal surface. This also improves paint adhesion by creating a micro-crystalline structure that bonds the paint more effectively.
-
-
Rinsing:
-
Another rinse follows to wash off any excess chemicals from the conversion coating stage.
-
-
Passivation:
-
To prevent flash rust or oxidation before the painting process, a passivation layer is applied. This stage may use a chrome-free or low-chrome product for environmental compliance.
-
-
Drying:
-
The pretreated parts are dried using hot air or infrared ovens to ensure all moisture is removed before painting.
-
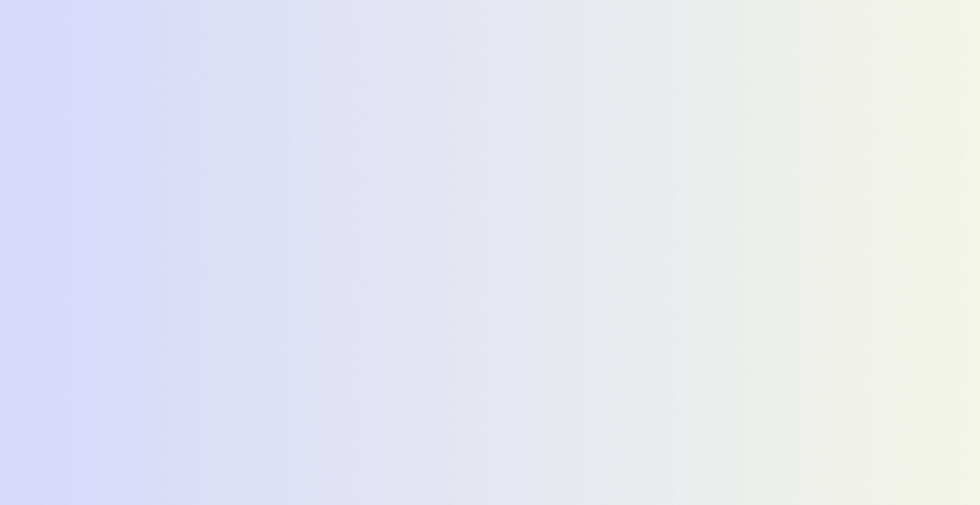
Environmental and Safety Considerations
Modern pretreatment systems are designed with sustainability in mind, utilizing eco-friendly chemicals, reducing water consumption, and minimizing hazardous waste. Many systems now employ closed-loop processes and filtration systems to recycle water and chemicals, reducing the environmental footprint.
Key Benefits of a Proper Pretreatment System:
-
Enhances coating durability and corrosion resistance
-
Reduces rework and defects during the painting process
-
Complies with environmental regulations
-
Increases operational efficiency and throughput
Industries That Benefit: Pretreatment systems are crucial in various industries, including automotive, aerospace, construction, and consumer goods manufacturing, where high-quality, durable paint finishes are essential.