E-Coat Systems

Overview
Electrocoating (E-Coat) is a high-efficiency process that applies paint or coatings using electrical current to deposit material onto a metal surface. It is widely used in automotive, appliances, and industrial sectors for superior corrosion resistance and uniform coverage. The system ensures precise coating even in complex geometries, offering cost-effective, environmentally friendly results. The E-Coat process involves pretreatment, immersion in a coating bath, electrical deposition, and curing in an oven.

Pretreatment System
-
Purpose: Prepares the surface for electrocoating by removing contaminants and enhancing paint adhesion.
-
Process:
-
Degreasing to eliminate oil and dirt.
-
Surface conditioning for uniform coating.
-
Phosphating to improve corrosion resistance.
-
-
Importance: Ensures the surface is clean and reactive, vital for strong adhesion and durability.
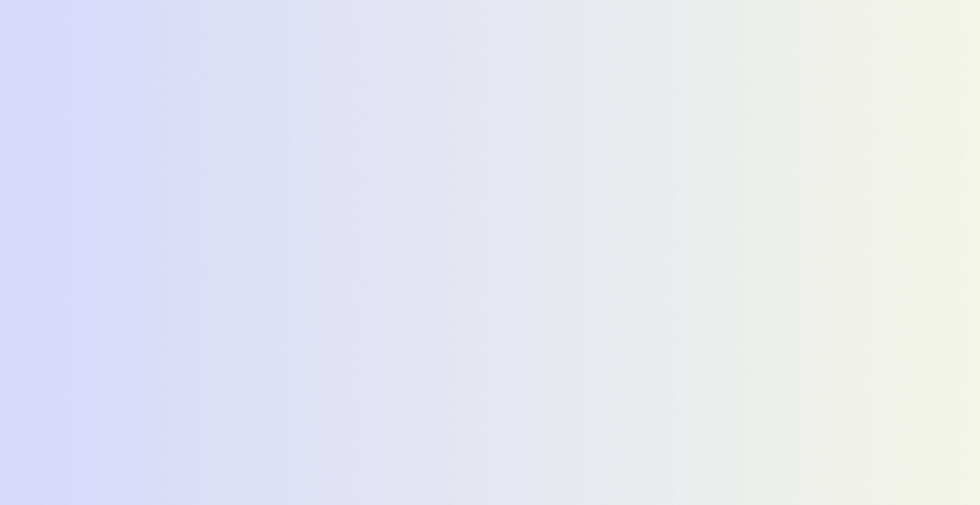
Coating Bath and Electrocoating Tank
-
Purpose: Immerses parts into an electrically charged bath for coating deposition.
-
Features:
-
Contains waterborne coating solutions (anodic or cathodic types).
-
Electrochemical reaction deposits paint uniformly, including in recessed areas.
-
Environmentally friendly with low VOCs.
-
-
Applications: Ideal for parts with intricate shapes, offering consistent coverage.

Power Supply and Control System
-
Purpose: Provides the electrical current needed for the electrocoating process.
-
Features:
-
DC rectifiers control voltage and amperage for precise deposition.
-
Adjustable settings to ensure coating thickness meets specifications.
-
-
Advantages: Maintains uniform application while minimizing material waste and rework.

Curing Oven
-
Purpose: Hardens the coating through heat, ensuring durability and adhesion.
-
Process:
-
Heated to specific temperatures to cure the coating material.
-
Achieves a smooth, hardened finish resistant to wear and corrosion.
-
-
Energy Efficiency: Modern ovens are optimized for low energy consumption.